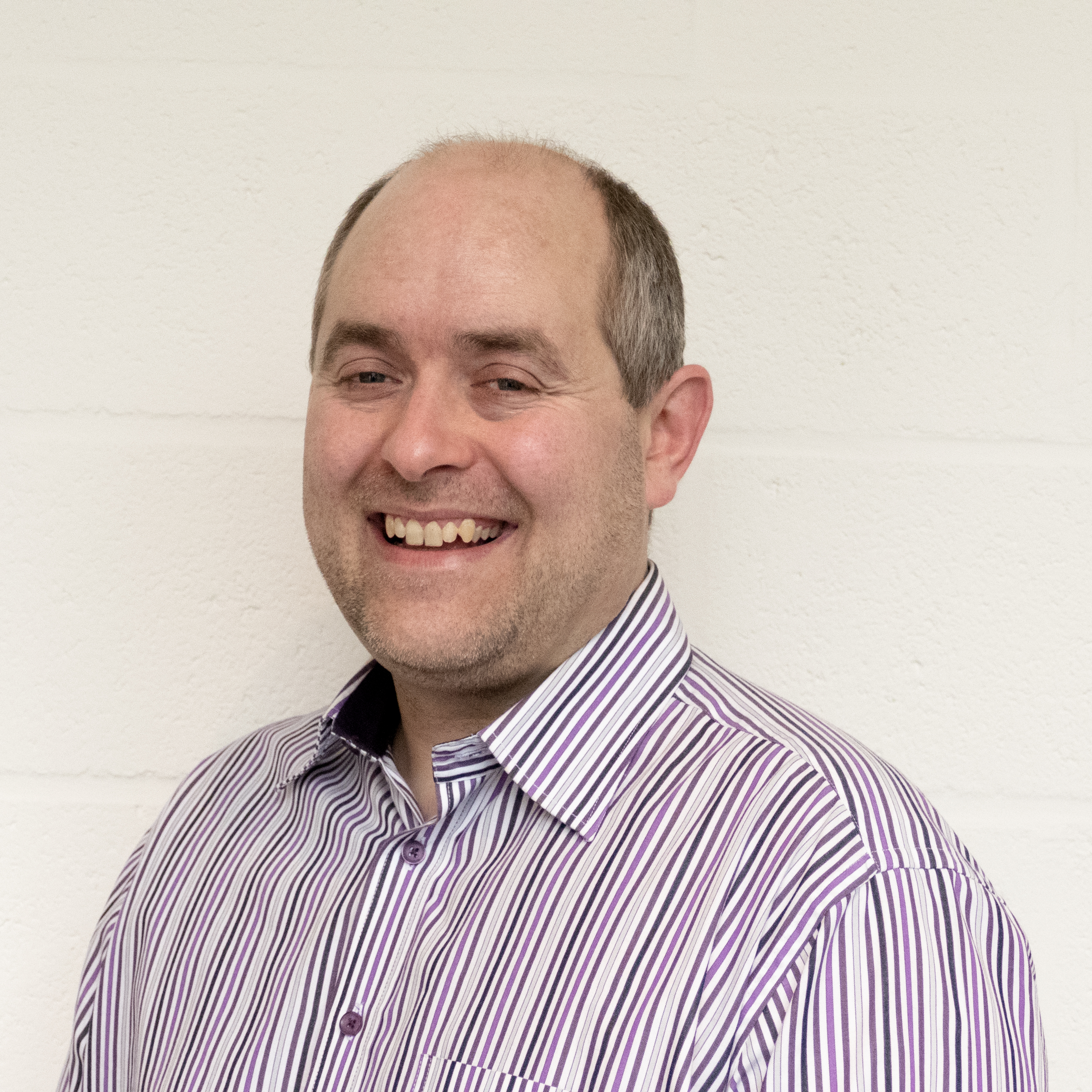
Track your chassis production with RFID
La Menuiserie Riche has always been at the forefront of technology. This family business has, as a particularity, the tracing of each frame through the various stages of manufacture in its facilities in Mariembourg.
Managing a frame manufacturing line is not as simple as it seems. The steps are numerous and the product variations are multiple. “We make custom-made products on an international scale” underlines Denis Hélénus, IT manager of Menuiserie Riche, “and we are capable of making complex joinery”. This family business, founded in the 1970s in Mariembourg, specializes in frames, exterior doors, curtain walls, etc. for professionals.
First the barcode labels
Between the raw material components and the chassis placed on the large frames before they are transported to the customers, it is a long way through the different workshops. From any PC, it is possible to follow the manufacturing process of each part.
“We started putting barcode labels on the frames at the end of the 90s,” recalls Denis Hélénus, “That’s when the collaboration with Etilux started”. The objective was to transmit information to the machines via the barcode but also to follow each frame in the factory to have a precise production trace with identifiable colors. Concretely, at each step, the manufacturing number on the label is used to go to the server to look for the specifics of the part to be machined. At the time, the size of the labels was adapted in length to contain a maximum of information. The media must also be comfortable to use and read.
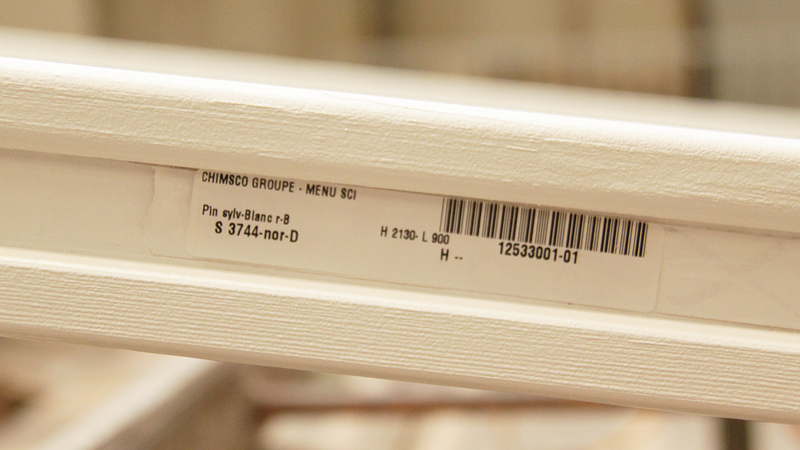
RFID facing the color challenge
The generalization of painting on the chassis changed the situation. While a large majority of them were impregnated with stain, the trend has been completely reversed: today, 80 to 90% of the chassis are covered with colors. Including labels! “It was necessary to work with RFID labels to preserve the traceability” underlines the IT manager.
While approaching the entry of the painting line, one observes the label posed by the operator at the beginning of the production line. The information contained on this RFID support ensures an identification and a follow-up on each of the machines during the various stages. At each scan, all the information is visible on the screen for the worker.
Technically, when he arrives at the painting line, a device reads the information on the label. At the exit, it is obviously no longer readable. The device then takes out a new paper label which is placed on top of the old colored label. The process can then be resumed with the useful information for the next steps, such as the installation of the hardware. This new “clean” label will also be useful to the customer since it indicates a specific reference for each joinery (bathroom, kitchen, etc.).
The transition to the assembly of the glazing brings an additional dimension. “The glass supplier also uses a label,” notes Denis Hélénus, “and so, by reading the barcode, it’s much easier to find the glazing(s) associated with the frame. The process continues until the end of the chain and boarding to the customer”.
In short, a simple and efficient system!
La Menuiserie Riche in brief
- La Menuiserie Riche, which celebrates its 50th anniversary this year, is specialized in windows, exterior doors, curtain walls…
- It is part of a family group, the Groupe Riche, which includes 2 other companies: Stabilame (manufacture and assembly of wooden houses and buildings) and Enercobois (manufacture of logs, pellets, dry firewood… from the waste of the other 2 companies).
- The joinery has professional customers: fitters, carpenters, contractors, … It also maintains close relations with architects.
- The Mariembourgeoise company currently employs 51 workers and 21 employees for a turnover of about 8.000.000 €/year.
Riche S.A.
Zoning Industriel, rue du Karting 5 à 5660 Mariembourg (Couvin)
Tél. : 060/31.00.50
accueil@chassisriche.be
www.chassisriche.be
Technical information
“The particularity of the solution lies in the space available to place the labels on the doors and frames,” explain Peter Haex and Isabelle Chelli, respectively Product Manager Traceability Solutions and Project Manager at Etilux. “The size of the labels has been adapted to fit the length of the doors and windows. They are designed to hold a maximum amount of information. The support must also be comfortable to use and read”.
The experience at Riche Carpentry shows the use of two technologies: scanning barcodes on printed labels in collaboration with IT Optics and then printing RFID labels, with Toshiba RFID printers that have a high printing speed. Advances in RFID technology guarantee performance and functionality at an affordable price.
“We are thus able to adapt to different situations. Another example is an equipment for a furniture rental company with the placement of RFID tags hidden under tables and chairs. We can therefore install traceability systems in a simple way”.
The solutions proposed by Etilux
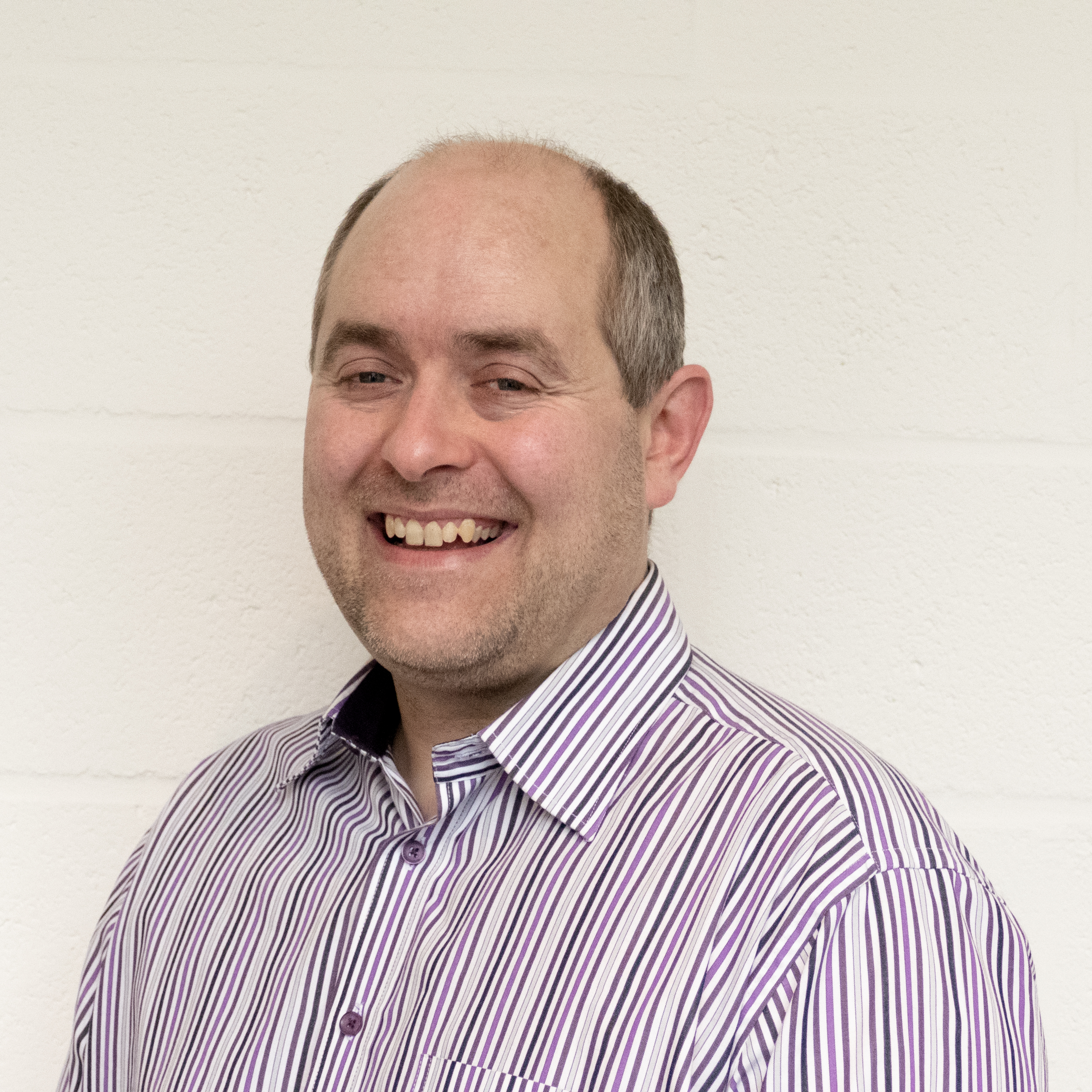
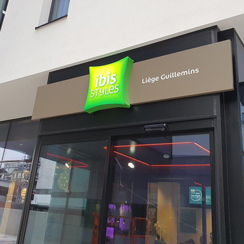
Ibis Liege Guillemins – Style and discretion
Discover our e-shop
A large catalog of products and services available 24/7